It's estimated that machinery downtime will cost around €92 billion in the EU in 2025.…
The power of the final mile in time-critical logistics
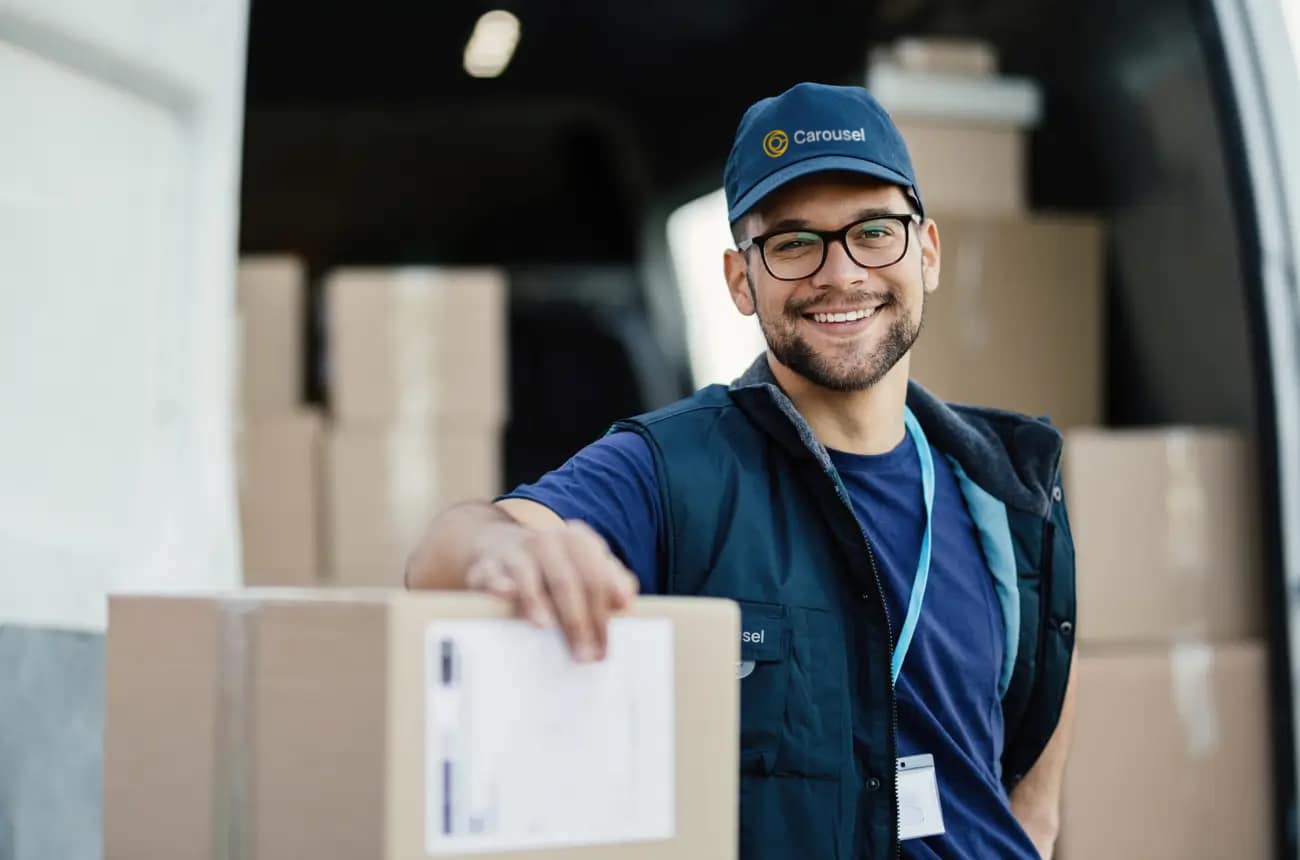
Efficiency is key – that’s true in business, not least in logistics. But there’s an overlooked advantage in the logistics operations that could unlock a whole new level of productivity and customer satisfaction.
It’s the final mile – the crucial stretch where parts arrive in the hands of your field engineers or dealers. And how it is managed can boost efficiency and build rock-solid customer loyalty. It’s time to take a look at how prioritising flexibility in the final mile can significantly improve your business efficiency.
Why final mile makes a difference
Imagine a field engineer stuck waiting for a critical part because the courier’s delivery window doesn’t align with the engineers’ schedule. When final mile options are rigid or limited, that’s exactly what happens. We all know that machine downtime can translate into lost revenue, potential fines for not meeting SLAs, and frustrated customers. A rigid final mile approach creates inefficiencies, hindering your team’s ability to perform at their best – and make the right impression on customers.
How flexible final mile options empower your business and build trust with your customers
- Dial down the downtime: Schedule deliveries around the engineers’ working hours, minimising waiting periods and maximising their ability to complete jobs efficiently.
- Superior customer satisfaction: Faster turnaround times for repairs and installations keep clients happy and loyal.
- Advanced agility: The unexpected happens. Flexible options afford you on-the-go adjustments, so you can keep things on track, allowing critical parts to reach the right place at the right time, minimising service delays. Our well-structured warehouse logistics network ensures inventory is strategically located to enable these fast and flexible deliveries.
Must-have components of a flexible final mile solution
Here are a few high-impact elements to consider when choosing your final mile options:
Time-targeted deliveries – This goes beyond basic delivery windows. By offering earlier and more specific delivery windows like pre 8:00 am, you can ensure that parts arrive precisely when they’re needed. This cuts delays and costly downtime, improving the engineers workflow and customers satisfaction.
Pre-planned placements – Predictability is powerful. Pre-planned deliveries that align with customer schedules means they’re not kept waiting unnecessarily. This optimises their time, allowing them to maximise their productivity, and their own success.
On-demand deployments – The unexpected is inevitable. But you can help your customers to respond to it through same-day or next-day critical parts deliveries. This minimises downtime and showcases your company’s responsiveness…and ultimately fosters trust and loyalty.
Convenient delivery locations – Traffic and travel eat into valuable time. Early morning delivery to a range of convenient locations, be it in boot, locker, PUDO or site, that match those of your engineers, is not only a game changer but offers greater flexibility and time in the field to make repairs.
Unleash flexibility, build loyalty
While efficiency is crucial, flexible final mile options can transform your supply chain operations significantly advancing your business growth, improving customers experience, and pushing forward your business overall competitiveness.
By prioritising flexibility in the final mile, you’re investing in the success of field service operation. At Carousel, we offer a range of final mile options to ensure seamless delivery, every time.
We offer a range of delivery solutions to ensure your spare parts reach their destination exactly when they are needed. Choose from direct-to-site, in-boot, or secure lockers and much more.
Want to know more?
Get in touch with our expert team to explore the best options for your supply chain.
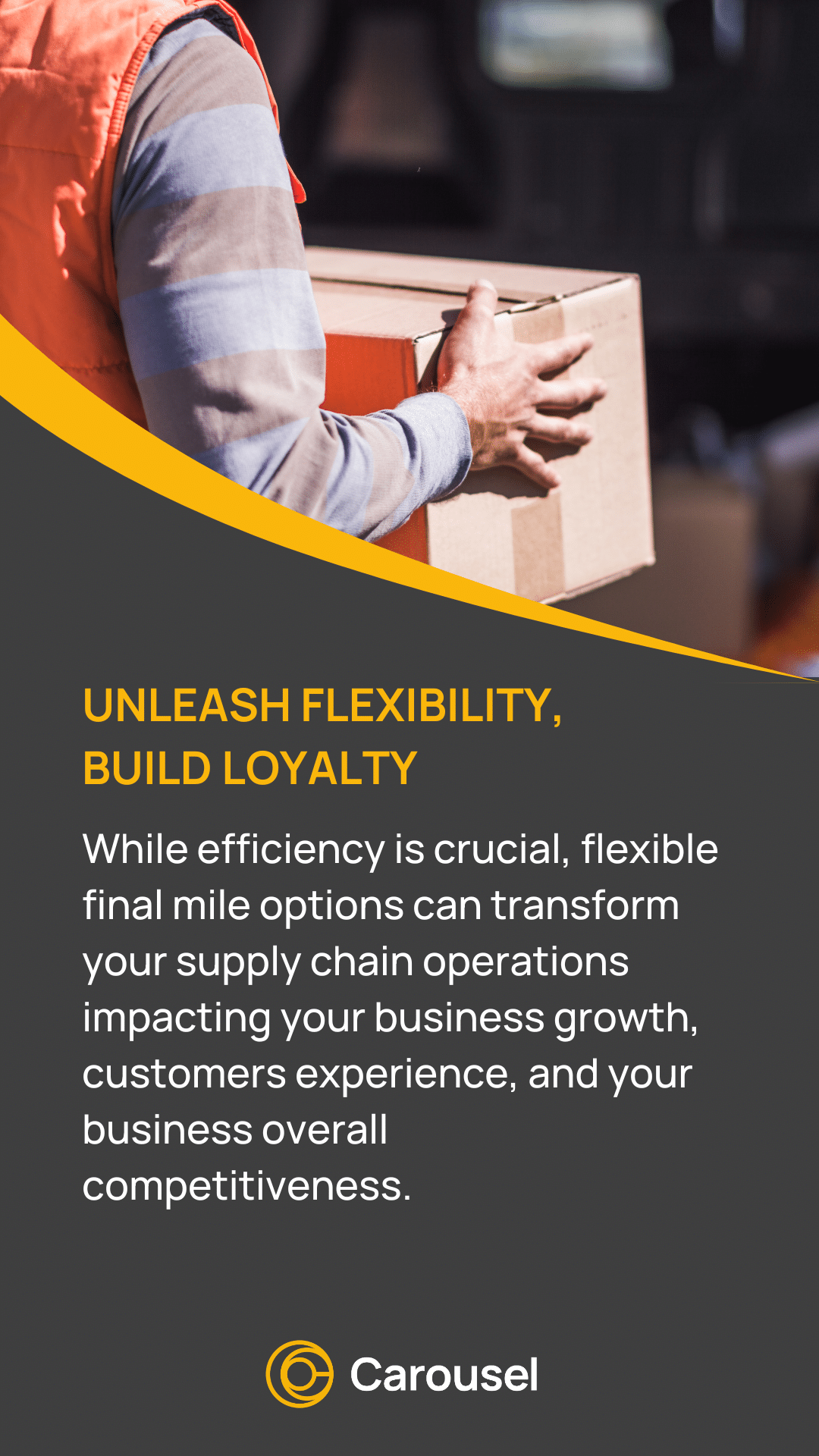