The energy sector depends on highly specialised, high-value equipment to maintain operations. As components like…
March 30, 2020
3 ways we’re keeping critical equipment moving across Europe
I’m an early riser and today’s current situation means that one of the first things I like to do is to check our company social platform. I like to see what everyone’s been up to, not just operationally, but because it helps me feel connected to my remote teams.
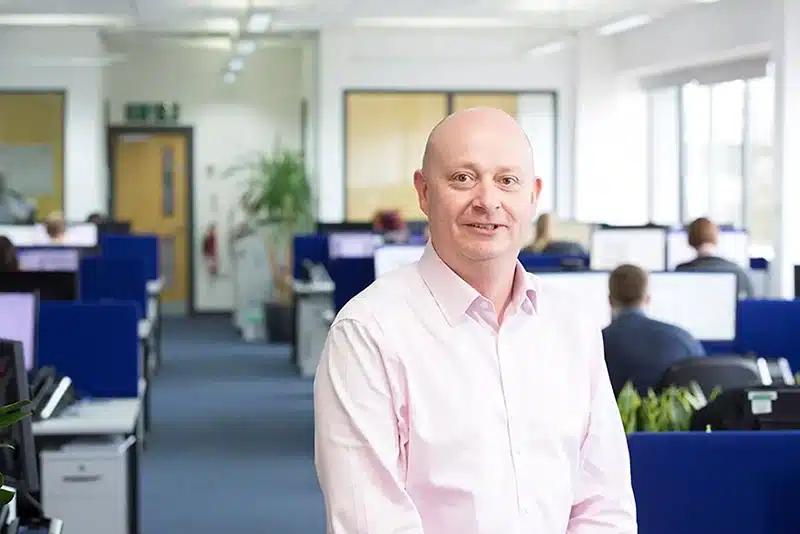
So, at 06.30 this morning, that’s what I did.
I was greeted with a video of our UK front-line teams working the night shift at our Coventry hub, paying a fitting, and what I found to be a quite emotional tribute, to the UK’s National Health Service*.
*NB. An 8pm ‘clap’ of appreciation was organised by volunteers in the UK on 26th. It saw everyone leaning out of windows to give all the ‘Health Heroes’ a well-deserved round of applause.
It goes without saying that the NHS, like all medical trusts across Europe, are doing a fantastic job in incredibly difficult circumstances.
The daily reminders we see of selfless and heroic work by frontline NHS staff prompted me to think about our own front-line teams and how they too, in our own way, are playing a critical role in delivering much needed and essential parts, products, medicines and equipment to where it’s needed most. So, here are just a few thoughts from me, on how we’re managing our operations, as this crisis continues.
Facing this unprecedented challenge
We, like many other providers, are on the front line of Europe’s response to the COVID-19 crisis.
High performance is what we do, so in some respects we’re always ready for dealing with supply chain challenges but, as someone said recently, there’s a lot of challenges we plan for – and are always ready for – but in reality, no one ever thought that we’d ever have to face every single one of them at once.
As this crisis unfolds, I continue to be amazed at how Team Carousel, across Europe, has reacted to the ever-changing situation. Each and every one has worked tirelessly to keep services operational, all the while working to strict new protocols and restrictions. Though we’ve had no COVID-19 in our ranks to date, we’ve still had to lean heavily on our teams – ensuring we maintain team safety, team culture and productivity, as well as the company’s strategic goals verses those individual battles on the front line.
I’m so grateful Team Carousel across Europe is made up of individuals that all share an attitude of working hard, doing the right thing and ultimately for getting the job done. Though we’ve been able to tap into our expertise, lever the power of technology and lean on our flexible approach to solution design and deployment, it’s our operational teams that have been the real heroes.
There have been three key challenges that have emerged as a result of COVID-19, here’s just a few insights on how we’ve approached them from an operations perspective.
1. Maintaining the safety of our teams
More than three weeks’ ago, we made the decision to segregate teams and send many of our office-based teams home to work remotely. Now, all non-operations staff are working from home, and maintaining the safety of our front-line teams remains a critical priority. I’m sure many of our teams back then thought it seemed like an overreaction, but strategically, we knew it was better to act quickly, than to risk it and do too little, too late. In actual fact, it was a move that put us in the best possible position.
As time goes on, we are continuing to follow guidance from leading authorities across Europe, including hygiene rules and safe distance measures, and we’re providing additional protective equipment to our front-line operations team wherever possible too.
It could be very easy for instance to just focus on the operations of a network, and the challenges that we face here and now, however in this heightened scenario we can see clearly that the welfare of our team and our client delight index are not mutually exclusive elements; they are very much intertwined in one another.
We’re managing this from a strategic point of view by monitoring sickness every day via our central CRM systems, and this means we can manage and contingency plan well in advance. By harnessing the power of data, we’ve been able to quickly assess teams in our daily huddles and make further precautionary actions – like sending ‘at risk’ team members home – but safe in the knowledge we can maintain our current services for clients without an issue. This activity is being supplemented by daily ‘virtual huddles’ with teams and the sharing of advice, updates and helpful ‘top tips’ via our social media platforms which all colleagues have access to.
2. Staying ahead of the curve (when things are changing by the day / hour / minute!)
Lack of supply chain transparency is something we’re always talking about with our clients and this current situation has really brought this to the fore. Businesses are often unaware of what’s happening across their supply chain, so they’re unable to know if or where issues could arise, and this makes it near-impossible to proactively manage and then navigate a situation like the one we’re in now.
It’s something that I know all too well.
Now I’m having to manage our operations team so closely, our ability to have 100% visibility across our operations, and the company, means we can be all the more efficient in our operations and contingency planning; and this is so important for both us and our clients right now.
In practice, we’re using more data-driven foresight than ever before to support our clients but balancing it with what many would call a more ‘traditional’ approach. We’re conducting daily calls to discuss current activity and contingency plans. ‘Service’ and ‘technology’ is a key differentiator for Carousel, and this is particularly important at the moment.
While data can give us a big picture overview, our strong client relationships have meant we can consistently adapt to changing situations that no one, or even a machine, could predict. For example, we’re adapting our solutions daily for one of our automotive clients because many of their dealers are needing to close or change their hours. These changes sit independent from our client and have been largely driven by limitations in dealers’ own resources, so that’s something we’re working closely with our clients to keep up to date and then establish a work around for.
It’s clear that communication has been key for us staying ahead of the curve and that’s where technology does play its part again.
Behind the scenes we are using a range of cloud-based data hubs, planning portals and reporting platforms – all aimed at keeping teams informed and aligned, at every minute of the day. We’re also now running a twice-daily video conference with key departments to monitor supply chains, intelligence share and make further contingency plans. These meetings mean we’re acting strategically, not reactively, and that everyone is being as efficient and effective with their time as they possibly can be.
3. Mitigating supply chain blockages
Flexible solutions I guess, is what many would say is Carousel’s ‘USP’. And it’s our long-established approach that’s helped us mitigate some of the supply chain ‘shocks’ we have been seeing.
Our solutions use a combination of our own infrastructure combined with services from those companies within our Trusted Network, and that means we’ve been able to switch-in alternative suppliers and amend order volumes as required during this time.
For instance, our freight-only flights, which run nightly in and out of mainland Europe, continue to operate, and this means that if necessary, it would be easy for us to swap a road service to a European air-connect solution if required. This flexible approach is particularly important as we continue to move parts and products from Germany, for our Medical and Healthcare clients, into the UK and Ireland. It goes without saying that these items are required urgently however we benefit from the ability to switch services to help meet those critical needs.
This model however wouldn’t be as effective if it wasn’t for the agile and flexible approach our teams have to tackling such challenges. It’s how I know that the efforts of our colleagues is what really will see us through this difficult time.
Final thoughts
When COVID-19 is brought under control, I fully anticipate that many companies will be focused on getting themselves ready for managing risk and keeping operations moving in times of extreme disruption. But in the meantime, if COVID-19 has taught us anything so far, it’s that ANY supply chain is vulnerable, but it’s how you react that’s the key.
Our teams are acting now and I couldn’t be prouder. I tip my metaphorical hat to all the key workers across the globe doing their bit, but particularly, to our wonderful teams across Europe.
If you need help, come and talk to us, we’d be only too happy to help.