The energy sector depends on highly specialised, high-value equipment to maintain operations. As components like…
Efficient construction logistics is essential to the successful completion of any operation, from residential and commercial projects to infrastructure works. must be stored and delivered correctly on time and within budget, and when these processes fail, disruptions are inevitable, leading to significant on-site delays and cost overruns. Let’s explore how the right spare parts logistics can be turned from a liability to a solution to mitigate risks and keep Construction operations on track.
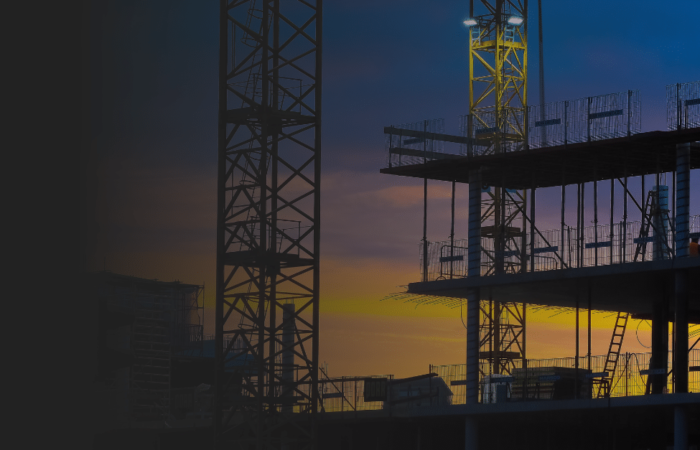
According to a report by McKinsey & Company, 98% of construction megaprojects experience cost overrun, and a total of 80% of projects exceed their original budget. Accurate scheduling, reliable deliveries, and reduced equipment downtime can be key to a successful construction logistics strategy, ensuring that projects are completed on time, within budget, and to the highest quality standards.
Precise Scheduling
The complexity of construction projects means that multiple trades work on different elements simultaneously, each with unique requirements and deadlines. Coordination is key to preventing disruptions that can delay a project. For example, an inaccurate estimated time of arrival (ETA), can lead to confusion and idle labour time, plus increased costs. The construction schedule must match the scheduled delivery of parts and equipment to increase efficiency. Therefore, it’s crucial that the construction schedule aligns with the delivery of parts and equipment to maintain efficiency.
Spare parts logistics plays a vital role in this process. A logistics provider that offers end-to-end visibility and control over all operations, from warehousing to deliveries, can ensure parts arrive precisely when needed, helping to keep the project on schedule. Engineers and technicians on construction sites can therefore have quick access to essential parts and machinery to avoid any delays in completing the project.
Reliable Delivery
Construction logistics face unique challenges, particularly when it comes to large and heavy materials being delivered to worksites that may be located in remote or urban environments with limited access. These sites are often busy environments, with restricted space that makes it difficult to unload and store materials, further increasing the risk of delays and damage.
A spare parts logistics provider who understands sector-specific requirements can help ensure a safe and smooth delivery process, guaranteeing that materials and equipment are correctly handled, stored, and delivered on-site.
Minimising equipment downtime
Equipment downtime can have far-reaching consequences in construction, causing delays, increased costs, and reduced productivity. Unscheduled equipment downtime could be due to broken parts or faults, quite different from planned downtime that can be necessary for preventative maintenance. Ideally, unscheduled equipment downtime should be kept to 10% or less, and equipment should be running at 90% availability or greater.
And that’s where seamless spare parts logistics becomes crucial. By ensuring the timely flow of spare parts with a wide range of final mile options and forward stock location (FSL) distribution strategies, logistics providers can maintain project momentum, enhance in-field productivity, and reduce extra costs associated with engineer services and unnecessary road miles.
Why choose Carousel?
When there’s no room for error in your spare parts delivery, you need a dedicated spare parts logistics solution. Our spare parts logistics solutions allow our clients to maintain consistent, on-time delivery of parts, even during peak times. Our services are tried and tested, flexible yet robust, designed to adapt to your specific project requirements across Europe. This means we work with you to develop the most appropriate supply chain strategy.
Ready to boost your construction logistics? Get in touch today to speak to a member of our sales team.
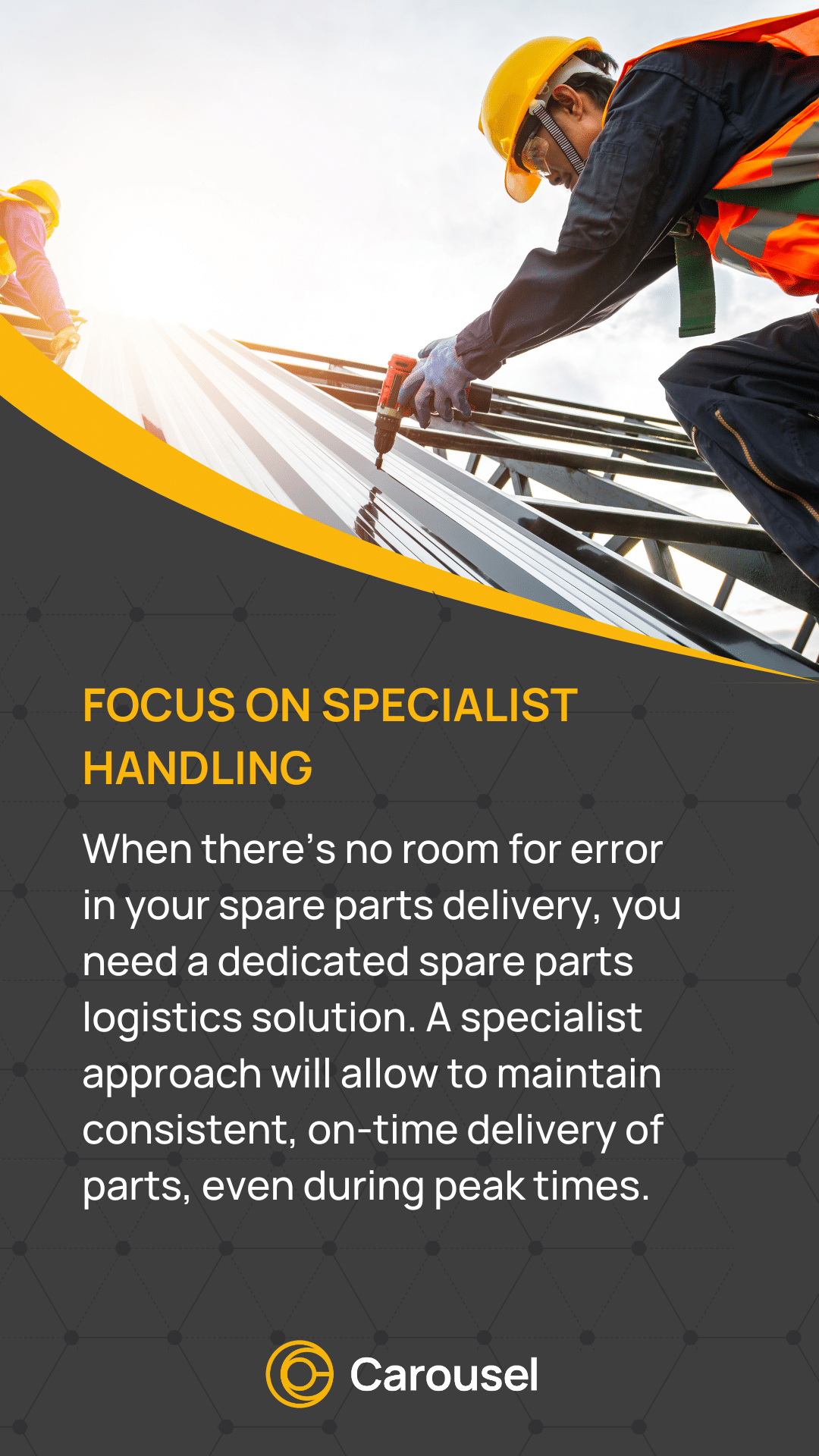